The manufacturing industry has been adopting various technologies to help reduce human intervention when performing manual and repetitive work. With the advent of digital technology, automation software programs play a big role in big data management that manufacturing companies also face as consumer demands increase over the years.
But how can manufacturing businesses benefit from using automation software? Find out the answer below.
1. Provides Accurate Manufacturing Daily Operations
Day-to-day manufacturing operations should be precise, yielding accurate results to reduce wasting raw materials and improve overall productivity. Automation plays a crucial role in ensuring these goals are achieved.
Automation promises tons of benefits for the manufacturing sector. For instance, an operator can return to the exact settings using a position-indicating hand wheel and position counter, which display the position of a control shaft accurately and eliminates the guesswork in the process.
2. Reliable Testing Automation
There are many ways automated technology helps businesses, including manufacturing companies benefiting from reliable testing automation. The other test automation attributes include maintainability, efficiency, portability, flexibility, usability, and robustness.
As manufacturers automate processes such as testing an applications’ performance using an automation tool, operators can focus more on other important aspects of their operations. An automated testing process allows faster and real-time data access of auditors, minimizing the risk of non-compliance.
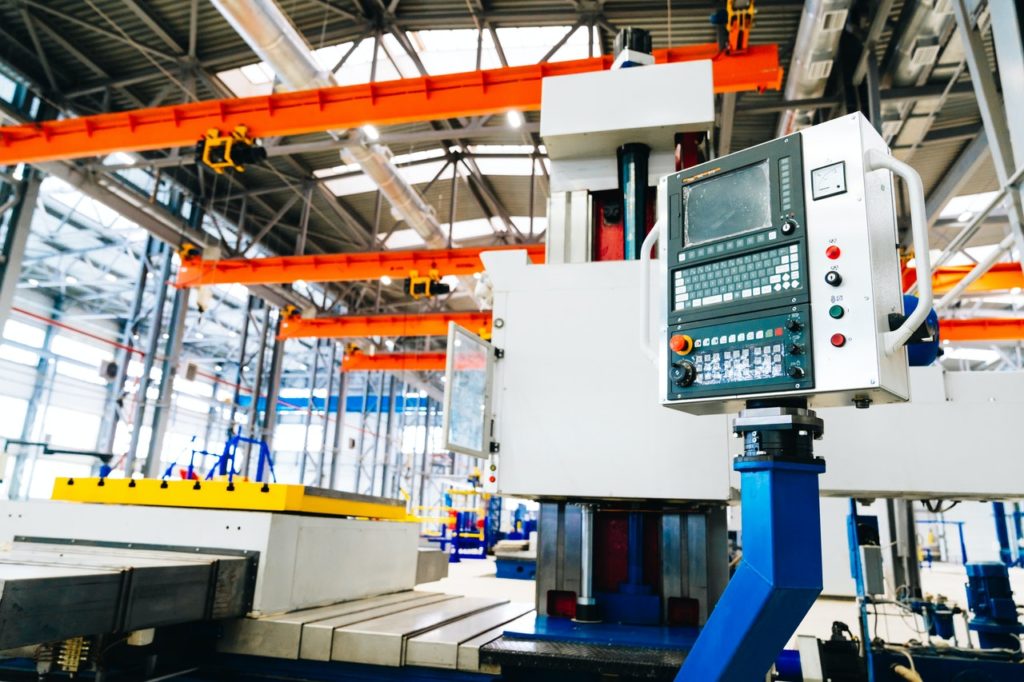
3. Increase Savings
A manufacturing business can save on employee salary and benefits and other costs associated with traditional manufacturing setup by utilizing automated software. Instead of spending time and money on resolving problems and issues, automation can improve efficiency and increase savings through digitized performance. And all these can be done without manual labor or human intervention.
By utilizing automated software, a manufacturing business can save on employee salary, benefits, and other costs associated with traditional manufacturing setups. Instead of spending time and money resolving problems and issues, automation can improve efficiency and increase savings through digitized performance. All this can be done without manual labor or human intervention. In particular, integrating automation with hot runners in injection molding systems maximizes the efficiency and precision in manufacturing thermoplastic parts, reducing waste and energy consumption.
Flexible, software-only automation software can work with a factory’s hardware to minimize costs. Such capabilities enable the pervasive adoption of automation in manufacturing companies.
4. Scalable Solution
Automation software programs promote the scalability of manufacturing businesses. With the globalization of industries, standardized testing and other processes are transferrable in various locations and settings. Automation software solutions can handle enormous data, accelerating operations without necessarily employing more people for the additional work.
Because of the higher production rates that automation offers, manufacturing companies can keep up with market demand and expand their reach. Therefore, manufacturing businesses can easily implement policies and standard operating procedures to align with the emerging needs of their clients and their company.
5. Track Defective Production
Product defects are a major culprit in any manufacturing business. It’s a good thing that manufacturers can now inject artificial intelligence (AI) into their inspection process as they turn the table to automation.
AI involves machines that simulate human intelligence processes that can help manufacturers improve inspections by tracking defective production automatically. Operators can program machines and set parameters that manufacturing equipment will follow to help detect product defects.
6. Accelerate Production
More than anything else, every manufacturing company strives to increase production to keep up with demands and satisfy suppliers and other stakeholders. Automating manufacturing processes can help accomplish this goal.
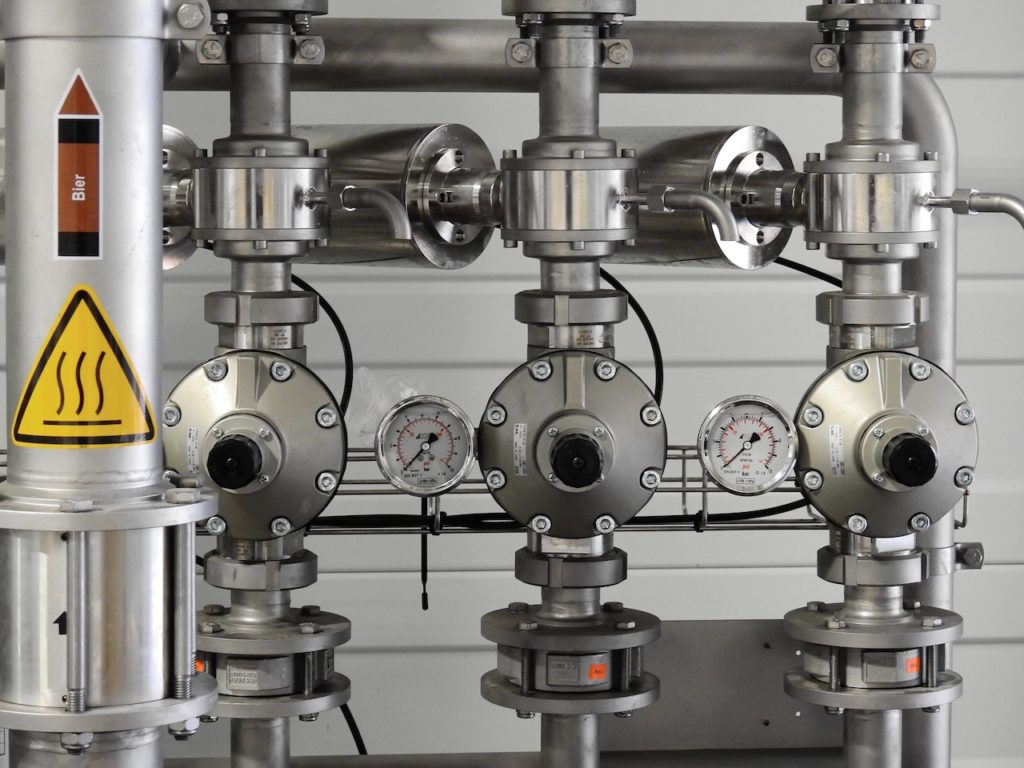
Here are the types of automation used in production:
- Fixed Automation: This automation is also called ‘hard automation,’ an automated production facility involving equipment-fixed processing operations. It means that the program commands are equipped in the machine, such as gears, cams, and wiring. Some examples are machining transfer lines in automatic assembly machines and the automotive industry, chemical manufacturing processes, painting automation processes, and material conveyor systems. Fixed automation promotes high production rates, so it outweighs high upfront costs.
- Programmable Automation: This automation involves manufacturing products in batches from dozens to thousands of units. Production equipment needs programming for each batch to meet new requirements. Some examples of programmable automation are industrial robots, programmable logic controllers, and numerical-control machine programs, coded and controlled in computer memory and program.
- Flexible Automation: This is a programmable automation extension, in which products are limited for automatic and fast changeover of equipment. The equipment reprogramming is carried out offline at a computer terminal. It means that the operator doesn’t use the production equipment itself. Flexible automation can produce a combination of different products instead of just one type of product in batches. There’s no production downtime and implementation of a made-to-order strategy is possible to customize products for clients. This is useful for businesses that allow personalization or customization of products.
Conclusion
Manufacturing businesses can benefit from automation software by drastically reducing manual work and improving production efficiency. This technology enables operators and managers to focus more on using accurate results and produce superior products. Now more than ever, manufacturing businesses can handle more data, product demands, and strict standard requirements.